
About Olson Floor Supply
Dream It
Family-owned and operated by three generations of the Nygaard family, Olson Floor Supply has been serving Long Island, New Jersey, Pennsylvania, Connecticut, New York City and up-state New York with high-quality, low-cost flooring, Benjamin Moore Paint, supplies, and equipment for over two decades.
We understand that the longevity of our business is based upon the satisfaction of our customers, that’s why we strive to bring the very best in product, price and service to those we serve.
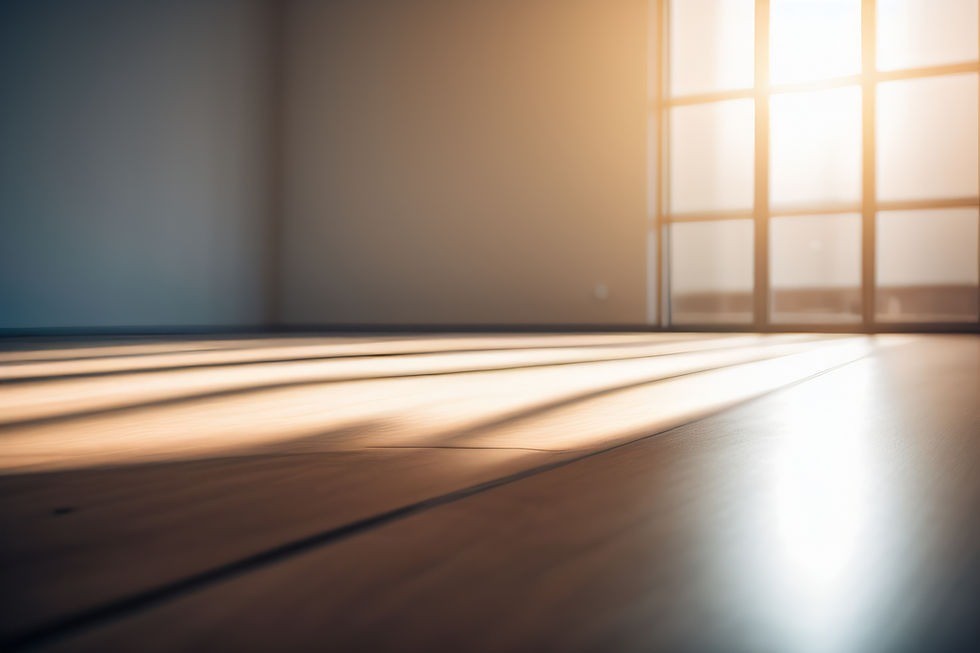
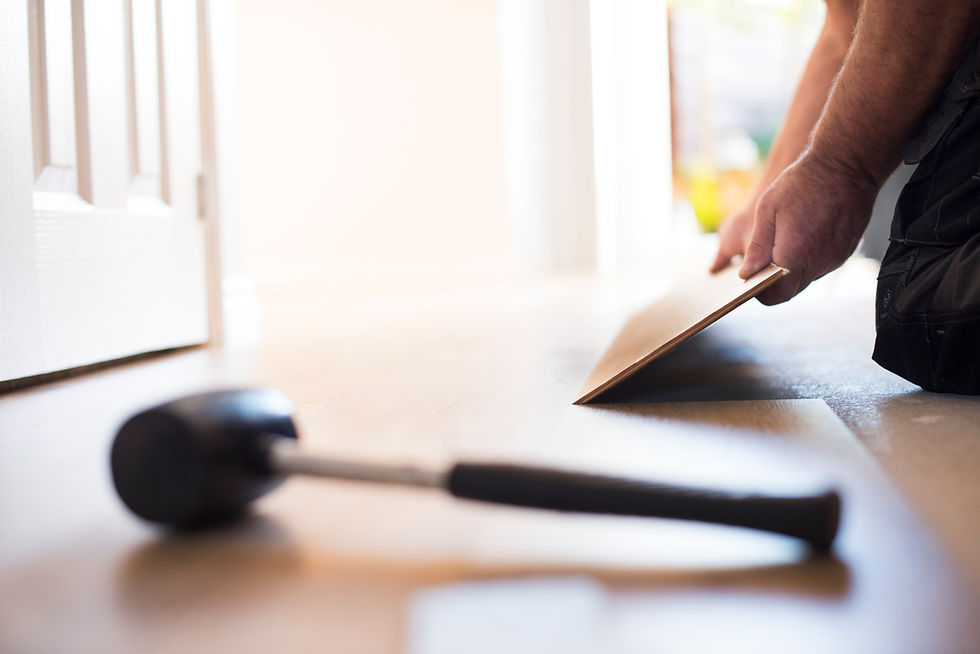
Build It
At Olson Floor Supply, our commitment goes far beyond providing high-quality products—it’s about creating a seamless and supportive experience from start to finish. We strive to ensure that every customer leaves with complete confidence in their flooring purchase, knowing they’ve made the best choice for their home or business.
Our dedication doesn’t end when the transaction is complete. We aim to build long-lasting relationships by offering unparalleled service, expert advice, and reliable support whenever you need us. Whether it’s your first project or one of many, we want to be the trusted partner you turn to not just today, but for all your flooring needs in the future.
One Stop Shop
We offer a complete range of services to meet all your flooring needs. From premium hardwood flooring and Benjamin Moore paints to supplies, tools, and machinery, we provide everything for your project. We also offer expert machinery repairs and personalized guidance to ensure your success.
Decades of Experience
With over two decades of expertise, Olson Floor Supply is a trusted, family-owned business committed to quality and customer satisfaction. Serving contractors, developers, and homeowners, we combine industry knowledge with personalized service to ensure every project is a success.
Accountability
At Olson Floor Supply, we stand behind every product and service we provide. Our commitment to honesty, reliability, and customer satisfaction ensures we deliver on our promises, making your success our top priority.
Our Services
We offer a complete range of services to meet all your flooring needs. From premium hardwood flooring and Benjamin Moore paints to supplies, tools, and machinery, we provide everything for your project. We also offer expert machinery repairs and personalized guidance to ensure your success.
Experience
With over two decades of expertise, Olson Floors is a trusted, family-owned business committed to quality and customer satisfaction. Serving contractors, businesses, and homeowners, we combine industry knowledge with personalized service to ensure every project is a success.
Accountability
At Olson Floors, we stand behind every product and service we provide. Our commitment to honesty, reliability, and customer satisfaction ensures we deliver on our promises, making your success our top priority.
Return Policy
1. All returns MUST be accompanied with original sales receipt.
2. NO RETURNS or EXCHANGES on items that are purchased at special pricing during a “CASH & CARRY” or “FINAL SALE.”
3. All material MUST be returned or exchanged in its original factory condition and packaging.
4. NO OPENED or TAPED boxes will be accepted for return or exchange.
5. All products MUST be returned within 30 DAYS of purchase
6. NOT ALL PRODUCTS are returnable OR exchangeable. Polyurethane, stains, paint, special orders, moisture cure, electrical parts, and machines are examples of some of the items that are not returnable or exchangeable!
7. All returns and exchanges are subject to a 15% restocking fee!
8. Cancellation of any orders including orders for stock items may be subject to a cancellation fee!
*NOTE: Any discrepancies or DAMAGE to goods must be reported to the OFFICE at the time of pick-up or delivery.
Return Policy
1. All returns MUST be accompanied with original sales receipt.
2. NO RETURNS or EXCHANGES on items that are purchased at special pricing during a “CASH & CARRY” or “FINAL SALE.”
3. All material MUST be returned or exchanged in its original factory condition and packaging.
4. NO OPENED or TAPED boxes will be accepted for return or exchange.
5. All products MUST be returned within 30 DAYS of purchase
6. NOT ALL PRODUCTS are returnable OR exchangeable. Polyurethane, stains, paint, special orders, moisture cure, electrical parts, and machines are examples of some of the items that are not returnable or exchangeable!
7. All returns and exchanges are subject to a 15% restocking fee!
8. Cancellation of any orders including orders for stock items may be subject to a cancellation fee!
*NOTE: Any discrepancies or DAMAGE to goods must be reported to the OFFICE at the time of pick-up or delivery.
Frequently Asked Questions
Engineered: Made up of several layers of wood. The top, or wear, layer of engineered flooring is the species you are purchasing (red oak, white oak, maple, etc.). The layers beneath might be of different species. Those layers are applied in perpendicular directions, adding stability to the floor. Generally suggested for installation over radiant heating or high moisture areas.
Solid: Solid piece of wood from top to bottom
Grain Pattern: Red Oak has a more varied or “wild” grain, with many swirls and deviations. The grain lines are also wider which can can give them a wavy or zigzag appearance. White Oak grain lines are smaller and tighter, making it look much straighter and uniform.
Color: Red oak has pinkish/red undertones while White Oak has brownish/tan undertones
Expect your floor to have natural variations in grain and color from piece to piece. That’s what makes real wood uniquely beautiful. We provide product samples and photographs to help with your selection, but your newly installed floor will vary from any samples or photos, because wood is unique.
NWFA/NOFMA certified flooring is graded in accordance with the NWFA/NOFMA specifications. Appearance alone determines the grades of hardwood flooring since all grades are equally strong and serviceable in any application. Boards are individually graded according to the natural characteristics of their appearance. Grades are determined by clarity, grain appearance, knots, dark stains, character marks and other features that might have been present in the tree. All characters included in a higher grade are automatically accepted in lower grades.
Select Grade: Contains all the variations in coloration produced by the contrasting differences of heartwood and sapwood. Also included are minimal character marks, such as small knots, worm holes, and mineral streaks, as well as slightly open characters. The combination creates a floor where the light sapwood and dark heartwood are combined with small characters and other small color interruptions.
#1 Grade: A flooring product characterized by prominent color variation that also contains prominent characters such as knots, open checks, worm holes, along with machining and drying variations. No. 1 Common is a tasteful floor where prominent variation is expected.
#2 Grade: Contains sound natural and manufacturing variations including knot holes, open worm holes, and other open characters along with prominent color variations. Manufacturing variations include drying characters and machining irregularities. No. 2 Common is most desirable for applications where numerous notable character marks and prominent color contrast is desired.
Select Grade: Random Length 1’-7’ With An Average Length of 33”
#1 Grade: Random Length 1’-7’ With An Average Length of 30”
#2 Grade: Random Length 1’-7’ With An Average Length of 24”
A. Storage and Conditions
1. Do not store wood flooring at the jobsite under uncontrolled climate conditions. Garages and exterior patios, for example, are not acceptable areas to store wood flooring.
2. Ideal interior climate conditions vary from region to region and jobsite to jobsite. It is your responsibility to know what your “ideal” climate conditions are and build your floor around those conditions.
B. Acclimation
1. Ensure that the building is enclosed.
2. Verify that the building is maintained at normal living conditions for temperature and humidity.
3. Where building codes allow, permanent heating and/or air-conditioning systems should be operating FOR AT LEAST 5 DAYS PRECEEDING INSTALLATION to promote proper acclimation.
4. If it is not possible for the permanent heating and/or air-conditioning system to be operating before, during and after installation, a temporary heating and/or dehumidification system that mimics normal temperature and humidity conditions can enable the installation to proceed until the permanent heating and/or air-conditioning system is operating.
5. Upon delivery, check wood flooring moisture content with a moisture meter to establish a baseline for required acclimation. Check the moisture content of multiple boards. A good representative sample is typically 40 boards for every 1,000 square feet of flooring. Acclimate to manufacturer’s recommendations or as necessary according to geographical location and your jobsite location.
6. Prior to installation, ensure that wood flooring is within acceptable range of moisture content with the wood subfloor. For solid strip flooring (less than 3” wide), there should be no more than 4 percent moisture content difference between properly acclimated wood flooring and subflooring materials. For wide-width solid flooring (3” or wider), there should be no more than 2 percent difference in moisture content between properly acclimated wood flooring and subflooring materials.
The ideal moisture content (MC) for hardwood flooring is about 6–9% when the indoor environment is 60–80 degrees Fahrenheit and 30–50% relative humidity.
Actual interior MC conditions in any location may differ significantly from these numbers. BE SURE TO ACCLIMATE THE FLOORING, CHECK THE MC IN THE SUBFLOOR, CHECK THE MC IN THE FLOORING ITSELF, AND CHECK THE RELATIVE HUMIDITY IN THE ROOM BEFORE INSTALLATION.